De-Alconox B
Dealcoholisation equipment for thermal dealcoholisation of beer
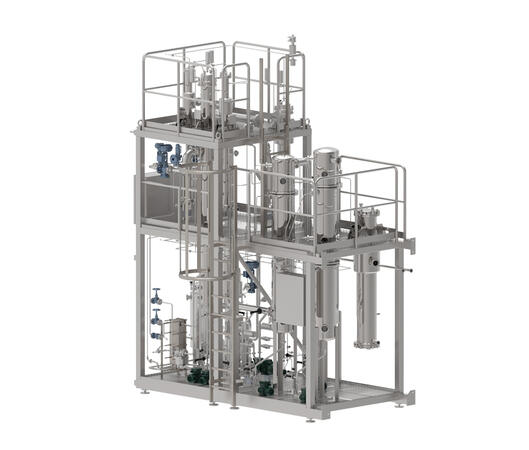
Thermal dealcoholisation of beer
Processing at lowest temperatures (< 39°C)
Dealcoholisation down to <0.02% vol.
Suitable for filtered and non-filtered beer
Bucher Unipektin dealcoholisation plants are designed in a way to produce a highly dealcoholised beer as well as rectified alcohol with minimum negative side effects on the beer quality. Additionally, the design is flexible regarding product flow and composition and is also well suitable for non-filtered beer. It makes it a sustainable investment for a brewery to serve all current or future market trends.
Firstly, the beer is gently degassed in order to avoid foaming throughout the process. The temperature of the incoming product is adjusted in counterflow to the outgoing dealcoholised beer.
Using a special Bucher Unipektin degassing system, very low final gas levels are achieved at a pressure slightly below the boiling pressure. The alcohol is then removed from the beer and rectified in a special column. The column consists of two sections: a first section for stripping the alcohol out of the beer and a second section for rectifying the alcohol to the desired concentration.
The unique design of the used high precision inserts provides several advantages:
minimum pressure drop allows a low temperature at the bottom of the column with minimal impact on beer quality and optimised energy consumption compared to similar systems
high tolerance for suspended particles enabling trouble-free processing of non-filtered beers
very low alcohol content achievable providing maximum options for final blending with non-treated beer
The energy for the stripping and rectifying column is supplied by a small amount of vapour which is evaporated out of the already dealcoholised beer. Bucher Unipektin uses evaporator bodies with a large heat transfer surface which minimises the required surface temperature in contact with the product.
Finally, the beer is cooled back and carbonised again. The whole process is operated under vacuum limiting the product temperature to 39°C and excellently preserving the quality of the treated beers.
Standardised dealcoholisation plants are available from 5 up to 200 hl/h.