Cerinox BR
Crossflow filtration plant with ceramic membranes for beer recovery from surplus yeast
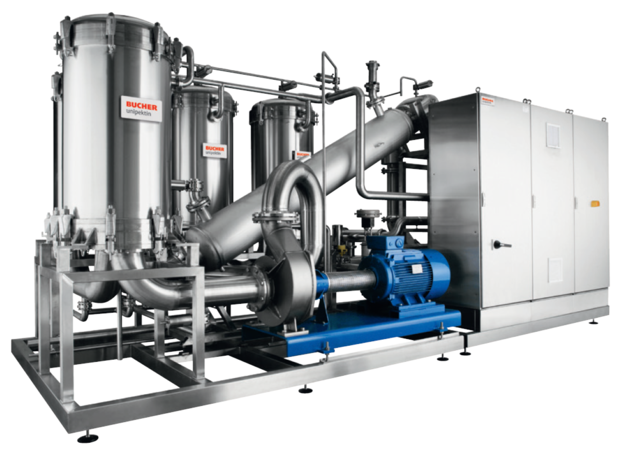
The Cerinox BR enables beer recovery from surplus yeast.
Short payback period
Economic system with diafiltration
High quality of recovered beer
During the brewing of beer, surplus yeast settles in the fermentation and storage tanks. The total volume of surplus yeast represents about 2-3% of a brewery‘s output. Approximately 50% of the volume of surplus yeast is beer, which is lost if the slurry is sent untreated to farms or food producers. If yeast is discharged into the sewerage system, very high treatment charges arise because of the very high biological oxygen demand. The average B.O.D. value is around 140,000 mg/kg. For these reasons, the valuable beer component should be recovered from surplus yeast.
Cerinox works according to the “batch principle”. While the yeast is recirculated through the plant and the batch (feed) tank, beer is recovered. Thanks to the batch tank, the concentration of the yeast increases slowly so that the plant works only for a very short period with the maximum concentration. The specific flow rate is increased by this type of process.
A semi-continuous operation can be achieved by substituting the volume of the recovered beer by fresh feed yeast slurry until the tank is filled with highly concentrated yeast. Diafiltration can be applied for increasing extract yield to increase the economic benefit. For these purposes, recovered beer is substituted by deaerated water. The remaining beer in the yeast slurry is continuously diluted so that beer with slowly decreasing gravity is recovered.
Cerinox is a compact cross-flow filtration plant equipped with ceramic tubular membranes. The plant consists of two main parts, the filter unit and the CIP station. Both parts can be arranged separately or on a common skid. Different automation levels are available, from manually controlled units up to fully automated plants.
The special design of the so-called dual-flow modules allows high packing density of filter surface, which leads to small footprints and lower heights of Cerinox plants. Especially because of the latter, the Cerinox is easy to maintain. Due to the compactness of the plant, its inner volume is small compared to the installed filter area. This leads to low water and energy consumption as well as low product losses.
Bespoke ceramic membranes for beer recovery from surplus yeast guarantee high economic benefit and high quality of recovered beer. The high durability of the membranes, together with our proven process - based on over 20 years of experience with more than 100 plants installed worldwide - leads to very reliable systems with minimal demand for operator presence and maintenance. This, and the short pay back periods, made the Cerinox a standard solution for beer recovery today.
Characteristics of the membranes
For the beer recovery process, tailor-made ceramic membranes in tubular multi-channel elements have been developed:
Channel diameter: 8 mm
Pore size: 0.3 µm
Pressure resistance: 30 bar
Temperature: > 90 °C pH 0~14
The robustness of the ceramic material guarantees long lifetime of the membranes, high availability of the plants, low membrane replacement costs and low maintenance costs.
Working principle
The cross-flow principle is characterised by the flow directions of the unfiltered and filtered liquid, which are perpendicular to each other. The preferably turbulent flow of the unfiltered liquid, which is parallel to the membrane’s surface, prevents particles from depositing on the membrane or carries away already deposited substances. So the throughput of filtered liquid through the membrane is kept high. A pressure gradient across the membrane forces the filtered liquid to penetrate the membrane.
The dual-flow module
The name of the dual-flow-module is derived from the two different flow directions (upwards and downwards) of the unfiltered liquid in the channels of the installed ceramic elements. Thanks to this concept, a maximum of packing density and a minimum of pipe connections are achieved. Complete venting and draining is guaranteed by discharging the liquid through the top and bottom plate. This concept allows for easy maintenance by simply taking away the top cover of the housing. With two different sizes of dual-flow modules - one with 20 m2 filter area, the other one with 48m2 – the filter area can be modularly increased, making it an optimal plant design for all required brewery sizes.
The maximum height of these plants amounts to 3.3 metres. The required floor space for the CIP station is around 2.5 x 1.0m. The required floor space depends on the number and type of dual-flow modules installed.
Some typical values for plants with the bigger type of module are:
Filter area/m2: 48, 96, 144
* Yeast/hl/day: 240, 480, 720
Space/m: 2.2 x 2.0 3.0 x 2.0 3.0 x 3.0
The membrane’s pore size of 0.3 µm guarantees high quality of recovered beer:
Turbidity of filtrate: < 08. EBC (90° angle)
Yeast cells in filtrate: < 5 cells / 100 ml
Bacteria reduction: > 105