Evaporators
Tubular falling film evaporator system for the production of concentrated fruit juices and aroma essences
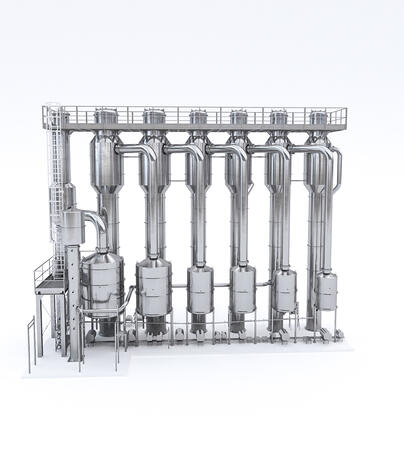
- Single-pass design for maximal product yields
- Energy-efficient multi-stage system
- Integrated, independently controlled pasteurizer
- Sophisticated liquid distribution provides for long cleaning intervals
- Optimized CIP with high performance spray nozzles
- Also available with MVR and TVR options as appropriate
Bucher Unipektin falling vacuum film evaporators are designed to produce high-quality juice concentrates and aroma essences. They typically combine the process steps of; pasteurisation, aroma-stripping and concentration in one system. Short processing time, low heat impact and sophisticated hygienic design make our evaporators ideal for the concentration of all kinds of fruit juices, i. e. from apples, pears, berries, grapes and stone fruits. Due to the uniquely designed liquid distributors they can handle juices with high suspended solids contents and with tartrate.
The evaporators are typically multi-staged systems. Energy efficiency can be improved further by using mechanical or thermal vapour recompression (MVR or TVR). Feed liquid is pre-heated with the concentrated product and condensed vapours in various heat exchangers for maximum energy efficiency in the evaporators. Before entering the first evaporation column the product can be pasteurised to a controlled temperature for microbiological and physicochemical stabilisation. The liquid is evenly distributed in the column head to ensure optimum wetting of the inner wall surfaces of all evaporation tubes. The tubes are heated from the outside with steam or recompressed vapours. The resulting product vapours push the liquid in a thin layer alongside the tube walls towards the separation chamber at the bottom of the column. Due to the applied pressure gradient, the preconcentrated product can be concentrated further in the next effect with the vapours from the previous effect. Optionally the first vapours are fed to an aroma column where they are condensed and refined to produce a concentrated aroma essence.
- Type: Vacuum tubular falling film evaporator
- Number of effects: 1 to 7
- Evaporation capacity: 10 to 110 t/h
- Vapour recompression: mechanical or thermal (optional)
- Aroma recovery: multi plate rectification column (optional)